
Complete Automatic Paint Production Line
Automatic integration coating complete equipment integrates automatic control, automatic feeding, high speed dispersing, recycle grinding, paddle-type mixing, automatic filtering, automatic filling, automatic gland, automatic modulating color, oil mixing and stacking. The system also includes recording parameter regularly, generating management reports, etc. which ensures the paint quality and upgrades the quality level , achieve the closed, constant, high efficient, automatic production.Application
8 Features of HUAYUN complete automatic paint production line
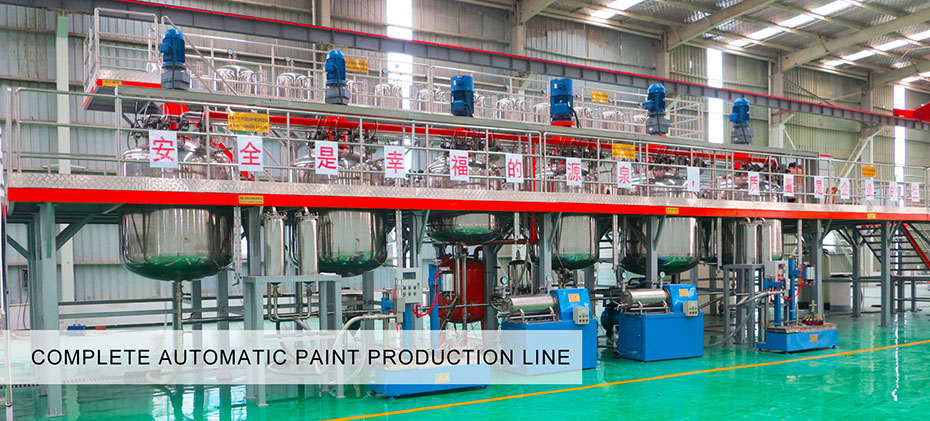
Feature 1 : Fully Closed Production Process
Fully closed production process has been adoptedto the automatic integration coating complete equipment.No leakage of dust pollution and organic solvent, thus it saves the loss of leakage and will not cause the air pollution. Production process is automatic intelligentized. Efficiency and quality are highly improved by monitoring and recording process regularly, adopting computermanagement model.
Feature 2 :Feeding The Material From The Tank Base
Feeding the material from the base by vacuum pressure makes the short feeding distance and feeding speed quickly.It avoid backflow and excavation which might happen if dothis job by labor. The material is surrounded by water after entering in the tank, this avoid the powder pollution into the air and blocking at the feeding port. It can feed 500kgs material to the tank within 2 min and keep the performance constantly. Traditional way is to feed material from the top of tank, It will take 25min to complete the same job, and the material is easy to adhere to the tank inwall causing the loss of material.
Feature 3: Double Layers Dispersing Disc
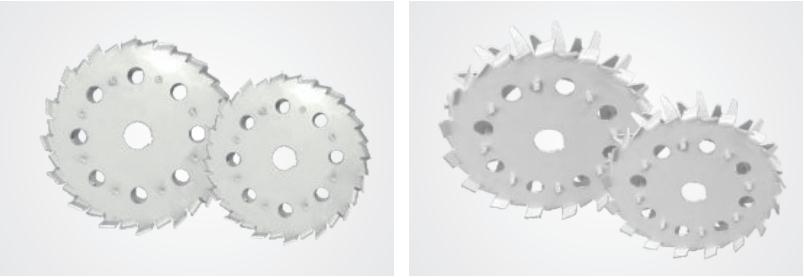
The key part of the complete equipment is the disperser and the key part of disperser is dispersing disc. Thus, Dispersing disc is very important to improve the dispersing efficiency. Double layer dispersing disc was adopted high wear-resistance material with high shear capacity and high speed. Efficiency of double dispersing disc is several times more than traditional type.
Feature 4: Fully Closed Manhole
The complete equipment requires transferring with vacuum pressure. If there is leakage point on the tank,the complete equipment will not work. We install the Sealing silicone on the cover of manhole, this operation avoids the material to contact with manhole cover making the sealing performance much better.
Feature 5: HMI、Automatic Production
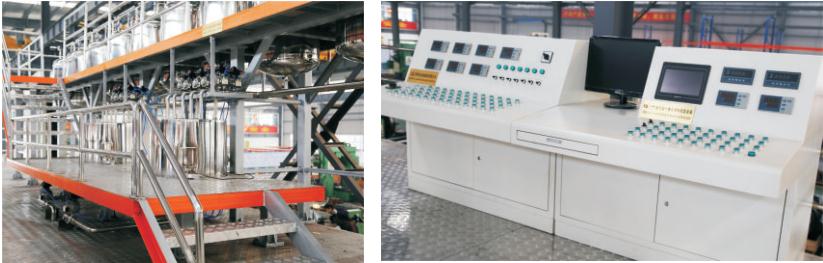
Microcomputer interface technique and automatic online monitoring are adopted to the production process. Material can be weighed automatically and precisely
Feature 6: Mechanical Sealing With Cooling Water
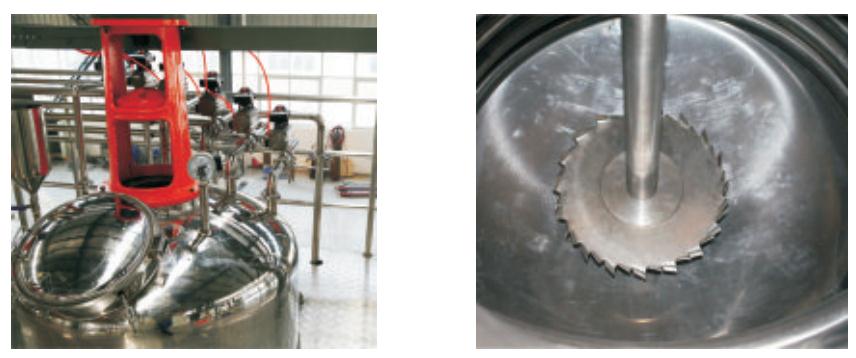
Traditional way is to use open mixing tank and feed material by labor. This way causes serious dust pollution. We adopts fully closed production process , feed material with vacuum pressure, and install the disperser in the tank, this way avoid dust pollution. High speed disperser is equipped with mechanical sealing with cooling water 、NSK bearings、flexible coupling、etc ,which ensures the quality and make it easy to do maintaining job.
Feature 7: High-precisionColor Mixer
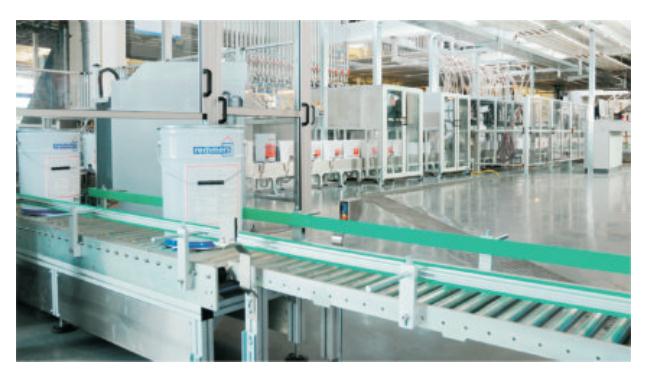
The color mixing processcontrolled by computer, avoids the cleaning of huge tanks, saves labor and time, improves the efficiency and achieves zero release. Automatically select, measure and inject, high automation, easy operation and simple maintenance. The packing tank position controlled by photoelectric sensor, more precise and reliable.
Feature 8: Recoil/bag Filter
Automatically remove the particulate impurities on the surface of the filter element through an efficient mechanical cleaning method, capable of on-line continuous filtration in a single machine, with an accuracy range of 25-3000 μm, without producing filter consumables, No need for frequent manual cleaning.
1. The straight-line reciprocating type removes impurities directly from the surface of the filtere lement.
2. The shaft seal adopts upper and lower two seals, good sealing effect, the disassembly and replacement are convenient.
3. On-line continuous filtration, automatic operation, end the heavy works of filter replacement and cleaning.
4. Less the filter pressure loss, flow is stable, reducing pipeline energy consumption, conducive to continuous and stable process.
5. Closed filter to prevent leakage of dangerous materials, which is conducive to the safe production.
Composition of complete automatic paint production line
Emulsion Feeding System
1.Emulsion Feeding Tank
The emulsion is transported by the tank truck into the plant and then pumped into the emulsion tank through a diaphragm pump
2.Emulsion Weighing
A. Set the amount of emulsion by computer. When it is required to enter the emulsion, the pneumatic valve for feeding the weighing tank is opened, and the corresponding diaphragm pump is interlocked .The emulsion is pumped into a weighing tank for weighing.
B. The computer controls the weighing tank. When the weight reaches the required amount of the formula, the feeding pneumatic valve automatically closes, the diaphragm pump chain closes, and the feeding stopped.
3.Emulsion Feeding Emulsion Feeding
Open the discharge pneumatic valve of weighing tank and feeding pneumatic valve of production tank , open the vacuum valve at the same time, and inhale the already weighed emulsion into the production tank by vacuum.
Additives Feeding System
1. Additives Loading
A. Additives storage tanks are equipped with a hydraulic meter and connected to a computer. When the liquid level in the tank is lower than the minimum level, sound and light alarms, indicating feeding. B. Open the vacuum pneumatic valve for vacuum. After opening the manual valves, inhale the additives agent into the additives storage tank. C. When the liquid level in the tank reaches the upper limit level, sound and light alarms, the vacuum pneumatic valve closes, and the manual valve is manually closed.
2.Additives Weighing And Calculations
Pressurize the additives storage tank, open the weighing tank feeding valve, and control the weight in the weighing tank through the computer. When the set weight is reached, the feeding pneumatic valve will automatically close.
3.Additives Feed
The additives is sucked into the production tank with negative pressure by vacuum.
Water Treatment Process

1.Reverse Osmosis Treatment
The tap water is treated by a reverse osmosis device before production, it is put into a pure water storage tank for storage and stand by after reaching the production standard,.
2.Cleaning Water
A. The part of pure water in the formula can be used to clean the residual liquid material in the liquid material weighing tank and pipeline to improve the weighing accuracy.
B. Set the amount of water in advance, open the inlet valve and the inlet diaphragm pump when cleaning, and pure water is pumped into the weighing tank.
C. The weigh tank is equipped with an automatic rotating cleaning ball connected to the inlet pipe, and water is automatically sprayed into the tank wall to rinse the residual liquid.
D. Open the corresponding material feed valve and vacuum valve and vacuum the residual liquid material into the production tank.
Pulping System

1. The powder is sucked from the bottom of the dispersion tank. The feeding distance is short and the speed is fast; it quickly mixes with the liquid, does not splash on the wall, and has no dust pollution.
2. Water, additives, emulsions and powders are mixed in a dispersion tank, and the dispersion time and frequency are set by computer.
3. The use of double-layer tooth-shaped strong dispersion disc, high shear force, high dispersion efficiency, it is a multiple times compare with ordinary dispersion disc.
4. Fully enclosed manhole, tightly sealed, unique structure to ensure production
Powder Feeding Process
1.Powder Material Loading And Storage
A. Open the air compressor and pulse dust collector and manually put the powder into the Powder pressure tank.
B. Open the corresponding valve, pressure the powder and sent to the powder silo (the powder silo is equipped with a powder level gauge, the computer displays the real-time material level, and there is sound and light alarm when the upper and lower limit material level), simultaneously open the dust collector in the top of the tank. When the upper limit level is reached, the loading valve closes automatically.
2.Powder Weighing And Measuring
A. Open the screw conveyor and conveys the pre-set amount of powder to the weighing tank for weighing.
B. The computer controls the weigh tank metering. When the weight reaches the required amount for the recipe, the screw conveyor automatically shuts down and stops feeding.
3.Suction The Powder Material By Vacuum
Open the weigh tank discharge and production tank feed pneumatic valve, open the vacuum valve at the same time, and inhale the already weighed powder from the bottom of the production tank by vacuum.
Paint Mixing System
1. The dispersed slurry enters into the paint mixing tank by the positive and negative pressure to mixing the paint. The stirring time and frequency are set by the computer.
2. The paint cans can produce different types of products, which can be filled into finished products to meet various needs of customers.
3. The paint mixing tank with paddle stirrer leaves, dispersing and mixing well.
Automation Control System
From industrial computers, DCS or PLC modules, industrial configuration software, cabinets, consoles, relays, AC contactors, thermal relays, air switches, etc. inUnder WinXP English environment, using the actual flow chart drawn by the industrial configuration software, the crew operation personnel can realize the operation of the unit through various screens displayed on the operation station for operation and monitoring. Each frame can display the real-time data of the weighing process variable and the status of the running equipment. The data and status update cycle is once per second.
Characteristics:
1.Hardware:
a. The main components of the system are customized or purchased from well-known manufacturers at domestic and abroad, are strictly used after screening.
b. All module cards are intelligent, using advanced production and manufacturing equipment and advanced detection equipment, with automatic correction function to ensure the system's control accuracy.
c. The system has a large load capacity: The total number of control tests can be within 20,000 points, fully meeting the requirements.
d. The main controller CPU of the system control station adopts advanced high-performance embedded industrial grade CPU chips (imported), and is configured in 1:1 redundancy (pair redundancy) to ensure maximum protection.Demonstrated the reliability of the control station.
2. Software:
a. Adopt advanced and optimized control software that can meet various control requirements.
b. The configuration and control software is easy to learn and use. The display animation shows the workflow and related animations. The operator can intuitively know the working status of the device. Just use the mouse to easily complete the production.
c. The system communication network adopts standard industrial Ethernet and has good openness. It can be connected to the enterprise management system through multi-functional stations and corresponding software.
d. The system can be configured online, debug online, and downloaded online, which greatly reducing the number of shutdowns caused by automatic control of the production system.
e. The parameters can be modified, saved, and recalled to the current work at any time to increase productivity.